Plastic-Injection Molding
Your Supply Chain Managed. Quality Guaranteed.
Plastic-Injection Molding
Plastic injection molding is the preferred process for manufacturing plastic parts, and tends to be ideal for people looking to produce a high volume of product. This process is usually used for thermoplastic materials, which can be easily melted, reshaped, and cooled for a desired design. Whether you need to manufacture automotive parts or food packaging, it’s important to find an overseas manufacturer that can meet your needs in a timely fashion. At United Global Sourcing, we can help you do just that.
While some companies simply connect you to a manufacturer and disappear, we put communication and quality and the forefront of everything we do. That’s why we maintain a 24-hour communication cycle with all of our clients, allowing us to quickly and efficiently identify any issues that arise during the manufacturing process. We understand that your needs are unique, and we’ll make sure your parts and components are assembled and delivered on time, every time.
High Volume & High Quality Parts At A Fraction of the Cost
When you work with United Global Sourcing for your plastic injection molding needs, you’ll be able to choose from a vast selection of thermoplastics and thermosets that meet your strength and function requirements.
We’ve worked with a variety of resins, including:
- Acetal
- Acrylic
- Acrylonitrile-Butadine-Styrene (ABS)
- Liquid crystal polymer
- Long-fiber reinforced plastics
- Nylon
- Noryl (PPO and PS)
- PC, PET, PE, PPS, PP, PS, PU, PBT, PEI, Peek and PTE
- Rigid and soft PVC
- Polysulfone
In addition to our injection-molded parts, we can also provide compression-, blow-, and roto-molded items as well. Check out our Industrial Manufacturing Gallery to see some of our recent projects!
Some of our popular plastic finishes include:
- Metallization (chrome, gold, silver)
- Painting (hand, screen, automated)
- Vacuum plating
- Lithography
- Custom texturing
- Hydrographics
Molded Natural Rubber/Elastomer Parts
You can obtain rubber-molded parts through either the injection or compression molding process. Rubber injection molding offers many of the same benefits of plastic-injected parts, including: low cost, high volume orders, and minimal finishing.
A Brief History of Plastic Injection Molding
A Brief History of Plastic Injection Molding
To give you a better understanding of plastic injection molding, it may be beneficial to look at the origins of this manufacturing process. The very first injection molding machines revolved around pressure die casting technology that was often used for metal processing. It wasn’t until the 1920s that a series of hand operated machines were introduced in Germany to process thermoplastic materials.
During this process, a lever was used to clamp a two-piece mold together, and molten plastic was injected into the mold to produce the desired shape or component. As an inherently low pressure process, the large-scale development of injection molding machinery did not truly occur until the late 1950s.
The Injection Molding Process
Today, the modern day plastic injection molding process has matured significantly. Most plastic injection molding machines are now fully automated, closed loop, or microprocessor controlled machines. The process of thermoplastic injection molding requires the transfer of polymeric material in powder or granule form from a feed hopper to a heated barrel. Once in the barrel, the thermoplastic material is melted and then injected into a mold. The mold is then clamped shut and is held at a temperature below the thermoplastic melting point. Within a short amount of time, the molten thermoplastic will solidify, and you’ll have the desired part.
Factors To Consider When Choosing An Injection Molding Material
Did you know that there are over 85,000 commercial options for plastic materials? In order to make sure you select the right resin for your injection mold, you’ll want to keep a few things in mind.
- Tensile strength - the ultimate tensile strength, or ultimate strength, measures a resin’s resistance to tension and its ability to withstand a give load without breaking or pulling apart.
- Impact strength - depending on the product you need to manufacture, some applications require more base strength or impact strength than others.
- Elasticity - This refers to the degree at which a material can be bent without becoming damaged.
- Heat deflection - Heat deflection is a very important characteristic to consider for applications that require insulating performance or a tolerance for high temperature ranges.
In order to select the best resin for your manufacturing project, you may want to ask yourself a few questions, such as:
- What is the intended end use of the part you are making?
- Does your product need to be flexible or rigid?
- Does your part need to be able to withstand pressure or weight?
- Will the parts be exposed to other chemicals or elements?
- Are their appearance considerations to keep in mind?
- Do you want to use a particular finish on the product?
Common Plastic Resins Used in Injection Molding
Once you find an overseas manufacturer to assist you with your plastic injection molding needs, you’ll have to decide on the type of plastic resin you’d like to use. Some of the most popular materials used include:
ABS (Acrylonitrile Butadiene Styrene)
Looking for a plastic resin with outstanding impact and mechanical strength? Acrylonitrile Butadiene Styrene, also known as ABS, can be used for a wide range of industries and applications. Many people like this resin because metal coatings can easily adhere to this material, making it suitable for products like phones, shower heads, and cabinet handles. It’s important to note that ABS does not have great chemical resistance properties, and you should avoid using this material in applications that require electrical insulation or UV resistance.
Popular applications: handheld devices, moldings for electrical tools, computers, remote controls, telephone parts, and cosmetic parts.
Acetal
Also known as Celcon, Acetal, is an ideal resin for a number of industries. This material offers incredible surface lubricity and chemical solvent resistance, and is ideal for food and beverage products, mechanical parts, automotive components, and household applications. This material should not be used for applications in high heat and temperature environments.
Popular applications: automotive parts, bearings, zippers, conveyor moving parts, gears, and pump and valve parts.
Polypropylene
Polypropylene is most often found in packaging but this resin can be used for several different applications. It’s very easy to inject this material into a mold, and it is highly resistant against other materials like acids and bases. With a high level of material strength, this can be a very cost-effective option for people who need plastic injection molds. It’s important to note that polypropylene is flammable and can be vulnerable to UV radiation.
Popular applications: fans, shampoo bottle tops, battery cases, paint cans, home storage options, and speakers.
High Impact Polystyrene
Looking for a versatile, economical, and impact-resistant plastic for your mold? High impact polystyrene, also known as HIPS, may be the right material for you. Normally used for low strength structural applications, HIPS offers great impact resistance, excellent dimensional stability, and tends to be very affordable.
Popular applications: gasoline tanks, computers, cups, toys, and automotive parts.
Polyvinyl Chloride (PVC)
Also known as PVC, polyvinyl chloride, is a resin that offers moderate resistance to impact, and has a low-to-medium strength and impact on mold. Known for its low cost, this resin is UV resistant and can be used to add strength to a variety of materials. It can also be used for containers, fencing, and other flexible parts.
Popular applications: electronics, automobile parts and components, wire and cable insulation, water pipes, household products.
The Top Benefits Of Using Plastic Injection Molded Parts
As we touched on above, the use of plastic injection molding has emerged as one of the best and most efficient methods to manufacture a variety of parts and products. As an effective way to mass produce a product or production element for your business, injection molding is as good as it gets when it comes to a speedy turnaround. There are many benefits to using plastic injection molded parts, including:
Detailed Features
If you’re looking to fabricate an automotive part or toy, plastic injection molding may be an excellent way to create the product or part you desire. Since the injection molds are subjected to extremely high pressure, it’s possible to create complex and intricate designs. Thanks to computer aided design (CAD) and computer aided manufacturing (CAM), it’s now easier than ever to include complex and minute details to your part’s design.
Quick Production Time
If you need to create a part or product and you’re pressed for time, you’ll be pleased to know that plastic injection molding can be an extremely fast process (especially when you compare it to other forms of manufacturing). While the speed of each production cycle will ultimately depend on the complexity and size of the mold, it should only take about 15 to 120 seconds between each cycle time. When there is a short amount of time between cycles, a greater quantity of molds can be produced in a short amount of time. This could mean increased revenue and profit margins for you, which is never a bad thing!
Enhanced Strength & Performance
Before you green light your plastic injection molds, it’s important to consider the strength of your part. The beauty of this manufacturing process is that it is possible to use fillers in the injection molds. These fillers can reduce the density of the plastic while it is being molded, adding more strength to the part after it has been molded. If your part or product needs to be strong and durable, plastic injection molding may be the best route to go.
Lower Labor Costs
If you’re looking to save money during the fabrication of your product, you’ll be glad to know that labor costs are typically very low in plastic injection molding. Since you have the ability to produce a variety of parts at a high-quality level with an incredible output rate, this can help with cost efficiency when it comes to your business. Most molding equipment today runs with a self-gating, automatic tool to help keep operations streamlined.
A Finished Appearance
Another major benefit of the plastic injection molding process is that there is little to no end finishing needed. This is because when the parts come out of the mold, they will be as close as possible to the finished appearance. This can be extremely beneficial, for both the turnaround time and the quality of your parts.
Minimal Waste
Did you know that the plastic injection molding process is actually very sustainable? Since most plastic materials can be recycled, there is far less waste within the original manufacturing process. This means that less plastic will go into our landfills and environment, which helps reduce the negative impact that plastics have on the world.
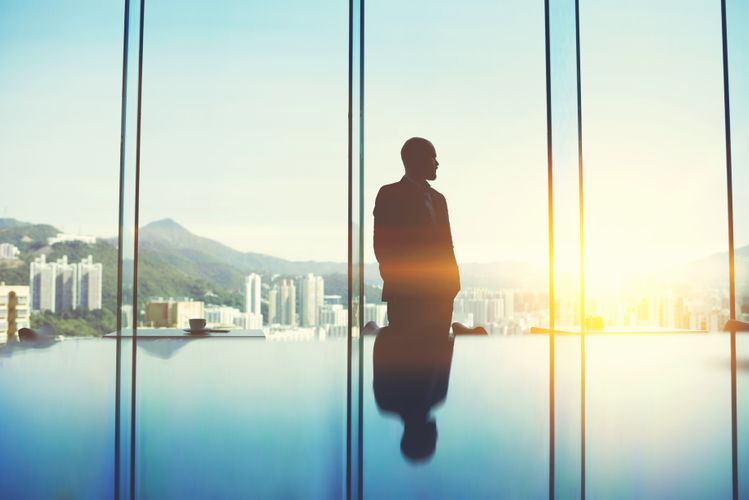
How Does Injection Molding Work?
- Every plastic injection molding process starts with a resin or raw plastic. The resin are initially dried and placed into what is known as a hopper, which is a reciprocating screw and barrel assembly.
- The raw plastic is then fed into the barrel, where it is simultaneously heated, mixed, and moved towards the mold by a variable pitch screw. The geometry of the screw and barrel are then optimized by an engineer in order to build up the correct amount of pressure.
- A ram then moves forward and the melted plastic is injected into the mold through what is known as a runner system, where it eventually fills the entire cavity of the mold. As the material starts to cool down, it resolidifies and takes the desired shape of the mold.
- Once the mold opens, you can push the solid part or component out with ejector pins. The mold will then close and the process will repeat.
- After the part is ejected, it is often dispensed on a conveyor belt or into a holding container.
The Two Sides of A Mold
When you work with a plastic injection molding company, you’ll quickly learn that there are two sides to a mold. There’s A side, which faces the front half of the mold or cavity, and B side, which faces the core or the back half of the mold. Each side serves a specific purpose.
- The A side often has a better visual appearance and can also be called the cosmetic side. The faces on A side will be smooth or textured, depending on your unique design specifications.
- The B side often contains important structural elements of the part and may include ribs, snap-fits, ad bosses. For this unique reason, the B side is known as the functional side. It will often have a rougher finish and possible visible marks from ejector pins.
Key Advantages of Injection Molding
- Plastic injection molding is the most cost-efficient technology when it comes to manufacturing high volumes of identical plastic parts.
- There is a very large range of plastic materials available for injection molding.
- Design requirements can be tailored to meet your exact needs.
- It’s possible to combine different materials into the same part for greater utility.
- The plastic injection molding process involves a high degree of automation which can provide significant savings in your production costs.
- There is very little material waste generated by this manufacturing process.
United Global Sourcing: Your Partner in Manufacturing & Fabrication
At United Global Sourcing, we offer turnkey solutions for all of your manufacturing and fabrication needs. From precision castings and machining to plastic injection molding, we can help you find the best manufacturer for your product. Get a free quote online today!
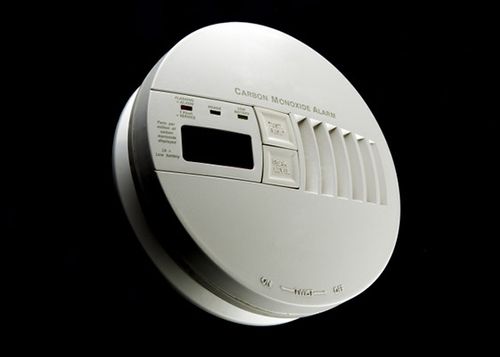
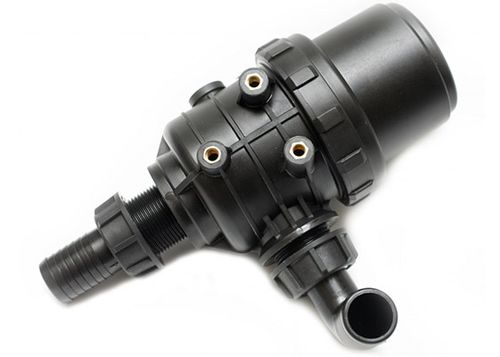
Contact us today to get started.
From simple to complex products, you can relax knowing your manufacturing requirements are handled by UGS.